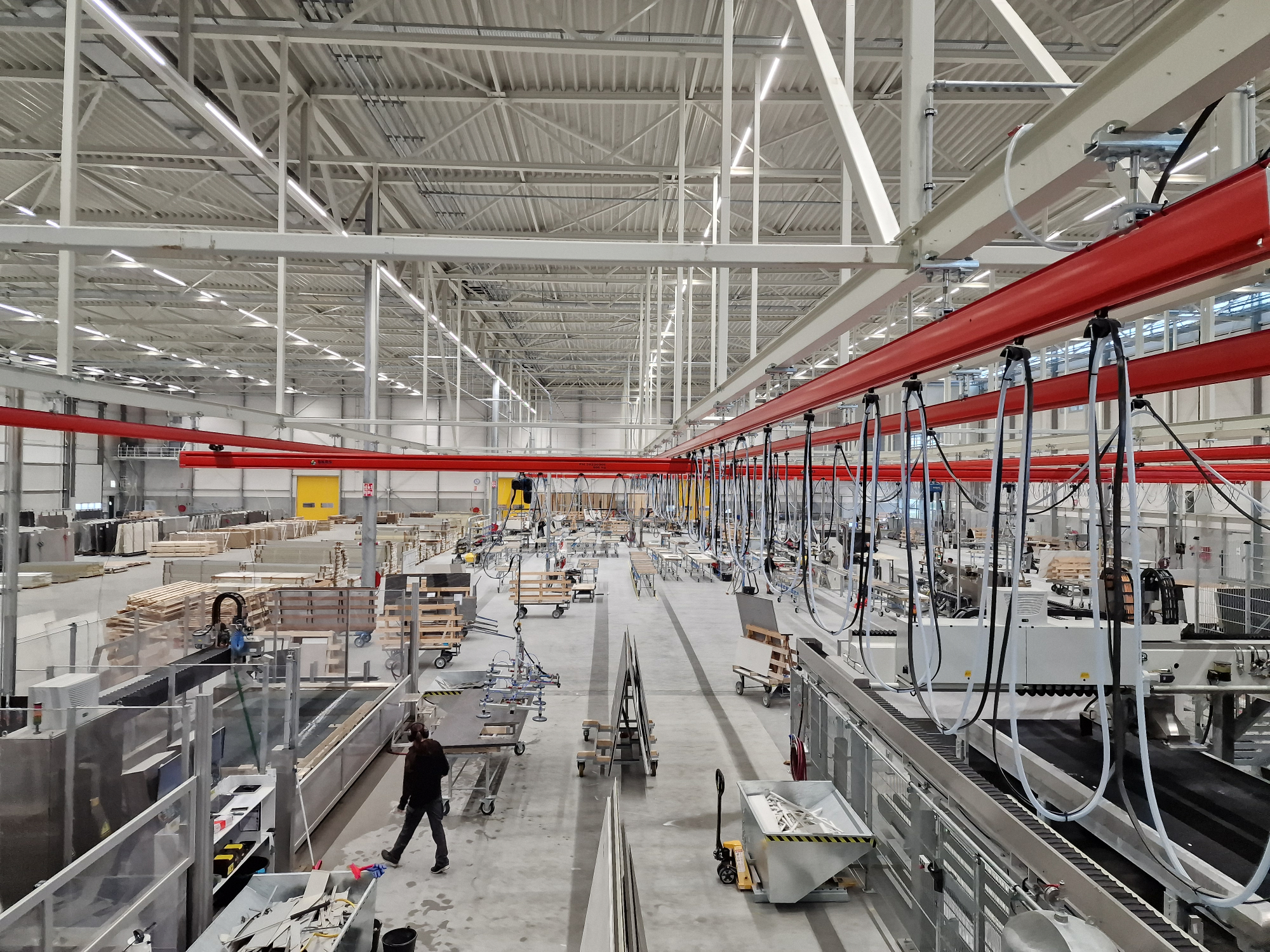
Begonnen op een boerderij, iets meer dan dertig jaar geleden, is Jetstone inmiddels uitgegroeid tot een van de grootste spelers op de markt van keukenbladenproducenten. Om aan de vooral internationale groei te kunnen voldoen heeft het bedrijf in Deurne een nieuwe hal van maar liefst 16.000 m² laten bouwen. Op de nieuwe locatie – een van de drie productielocaties in Deurne – is een state-of-the-art productielijn opgebouwd. De komende tijd worden de kantoren en het moderne trainingscentrum voor medewerkers en klanten ingericht. Een gesprek met directeur John van den Heuvel over de ambities van het bedrijf. En over de tegenslagen waarmee het bedrijf te kampen heeft gehad.
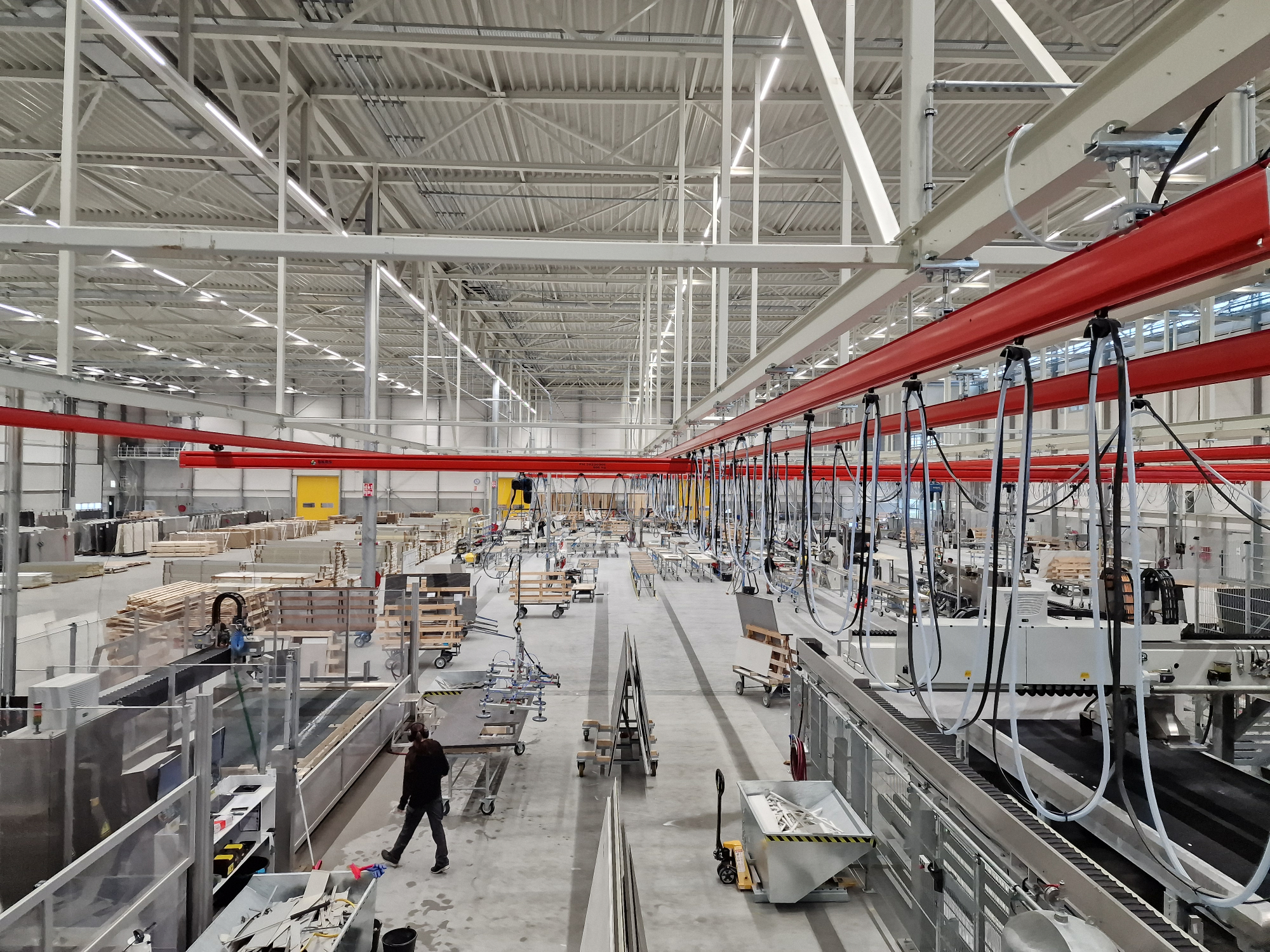
“Welkom in ons ‘Gelredome’”, zegt John van den Heuvel joviaal. Hiermee refereert hij aan de vorm van het nieuwe gebouw dat door Pepers Architecten uit Helmond is ontworpen. “Net als het stadion van Vitesse. Maar onze prestaties zijn beter”, voegt hij er met gevoel voor understatement aan toe. Daar waar de voetbalclub uit Arnhem vecht tegen degradatie, heeft Jetstone uit Deurne juist een flinke sprong op de ranglijst van producenten van keukenbladen gemaakt. Met de nieuwe productiehal erbij verlaten wekelijks zo’n negenhonderd à duizend bladen de drie productielocaties met nationale en internationale bestemming. “Allemaal maatwerk, wij produceren niet op voorraad. De keukenbladen gaan naar onze klanten in Nederland, Duitsland, België, maar ook naar onze eigen vier locaties in Zweden. Daar werken zo’n veertig medewerkers, zij verzorgen de levering en montage van de keukenbladen. Oorspronkelijk leverden we ook aan het Verenigd Koninkrijk, maar daar zijn we na de Brexit mee gestopt”, legt Van den Heuvel uit.
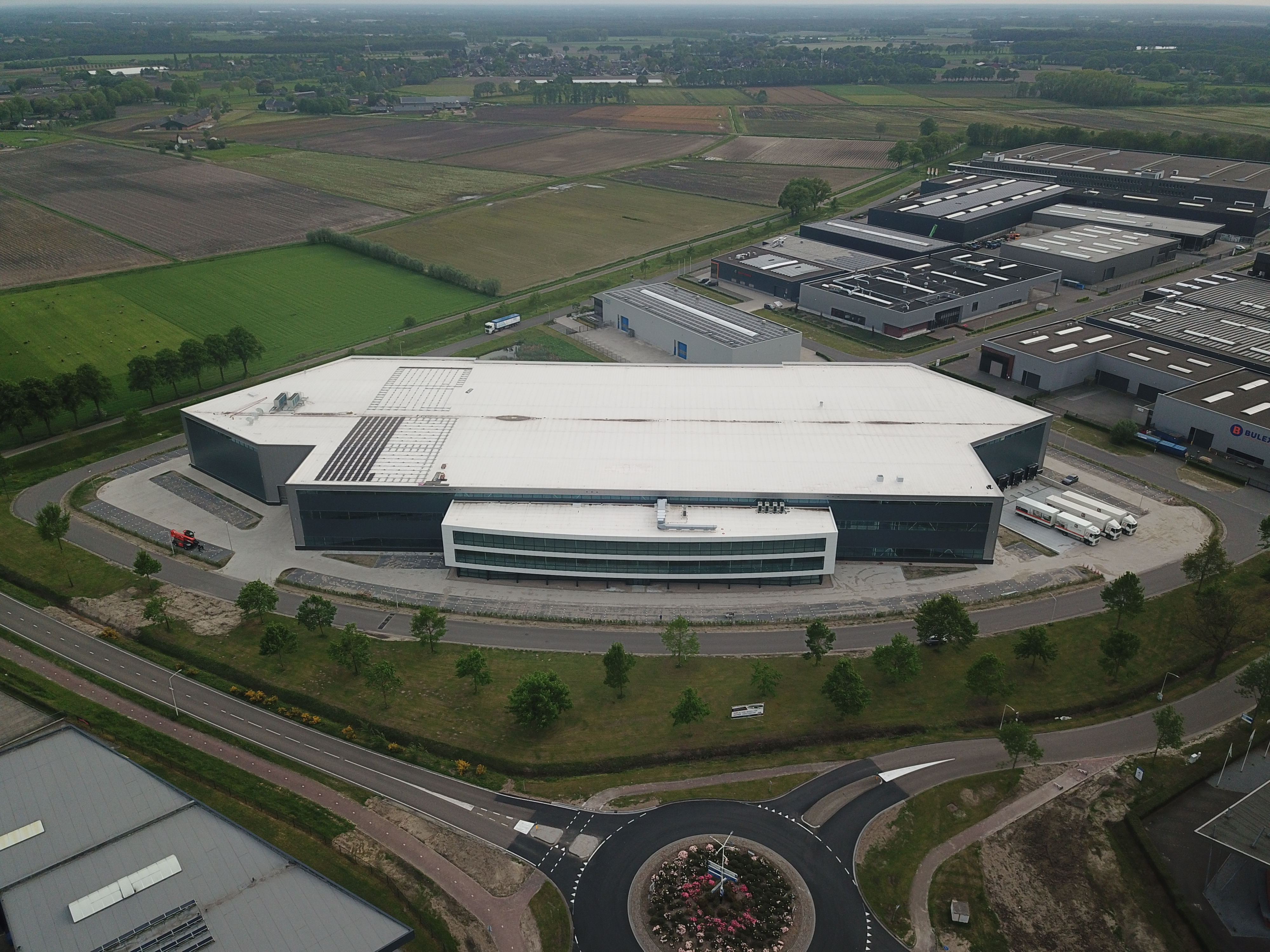
Boer
Het verhaal van het succesvolle bedrijf uit Deurne begint in 1993. Jan van den Heuvel, de vader van John, legde een natuursteen vloer bij boer Nooyen in Deurne. “Tijdens het werk raakten ze aan de praat over de hoge prijs van die natuursteen vloer. Dat moest volgens hen veel goedkoper kunnen.” Ze staken de koppen bij elkaar, samen met Peet Veldhuijzen, die op dat moment nog bij Kemie in Asten werkte, een gerenommeerde producent van natuursteen keukenbladen. “De landbouwvoertuigen gingen eruit en de machines om natuursteen te bewerken kwamen erin. Letterlijk naast de mestvarkens werden de eerste keukenbladen geproduceerd. Klanten en leveranciers wisten het bedrijf direct te vinden; bij kilometerpaal 0.5 rechtsaf en over het zandpad naar de productielocatie”, legt Van den Heuvel uit. En dat er uitsluitend keukenbladen werden geproduceerd, was van begin af aan duidelijk, voegt hij eraan toe. “Veldhuijzen zei dat natuursteenbedrijven die grafwerk produceerden en/of leverden vanaf begin oktober tot en met begin november nauwelijks productie konden draaien. Dan stond alles in het teken van Allerheiligen en Allerzielen, het onderhoud aan de graven en de grafmonumenten stond in die maand voorop. Je kunt beter die tijd gebruiken om volop productie van keukenbladen te draaien, was de overtuiging van Veldhuijzen. En daar kreeg hij gelijk in.”
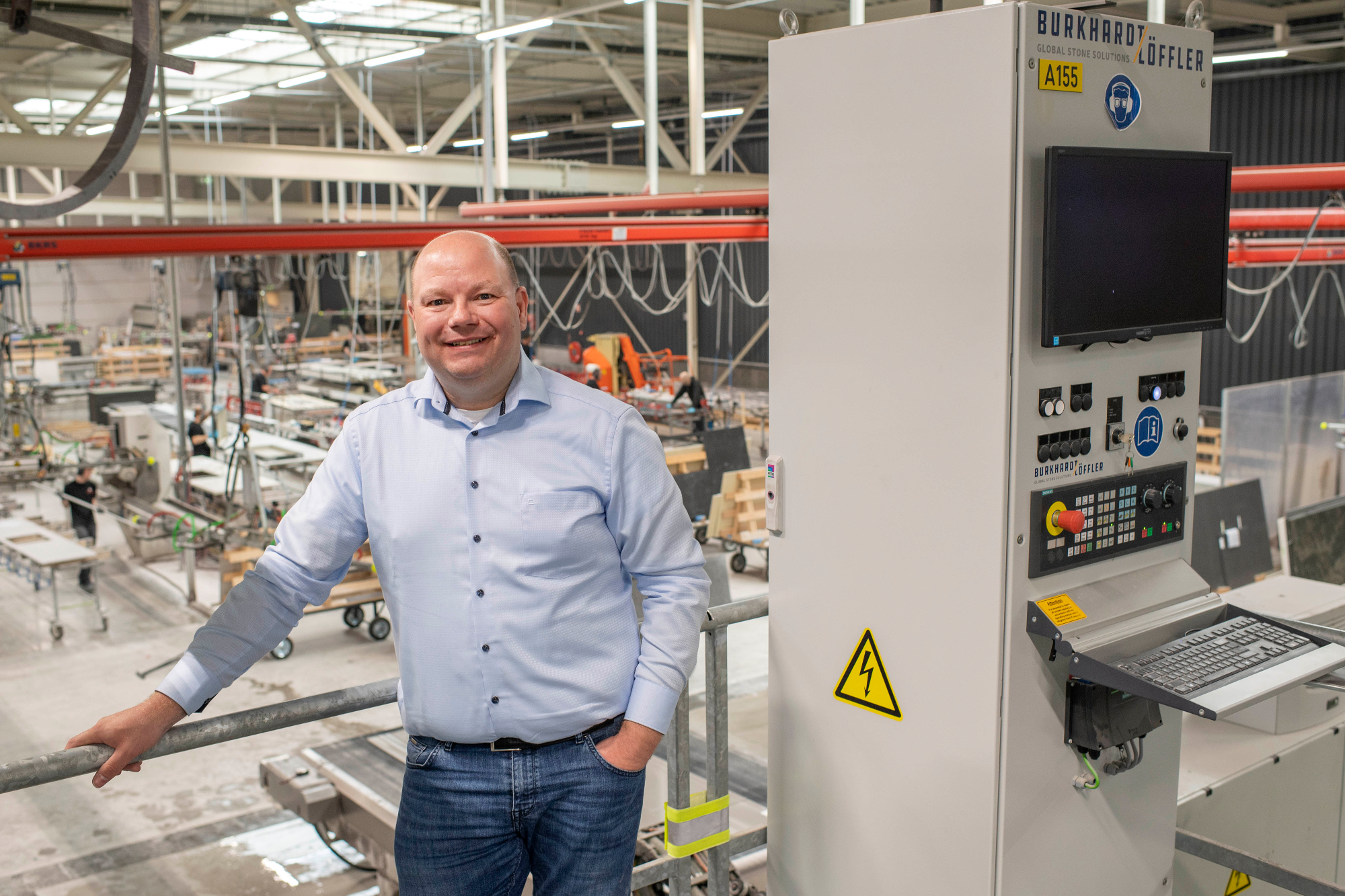
Flintstones
Het nieuwe natuursteenbedrijf werd Jetstone gedoopt. Daar zit een mooi verhaal achter, vertelt Van den Heuvel. “Al snel werd gedacht dat de naam te maken had met het snel leveren van natuursteen producten. Niets is minder waar. Het oorspronkelijke idee was om het bedrijf Flintstone Natuursteen te noemen. Dat mocht echter niet van Hanna-Barbera, producent van de tekenfilmseries van The Flintstones over de belevenissen van een gezin in het stenen tijdperk. In diezelfde tijd had je een tekenfilmserie The Jetsons, ook geproduceerd door Hanna-Barbera. Daarbij kwam dat de vrouw van de boer Jet heet. Dit alles bij elkaar samengevoegd leverde de naam Jetstone op”, legt hij uit.
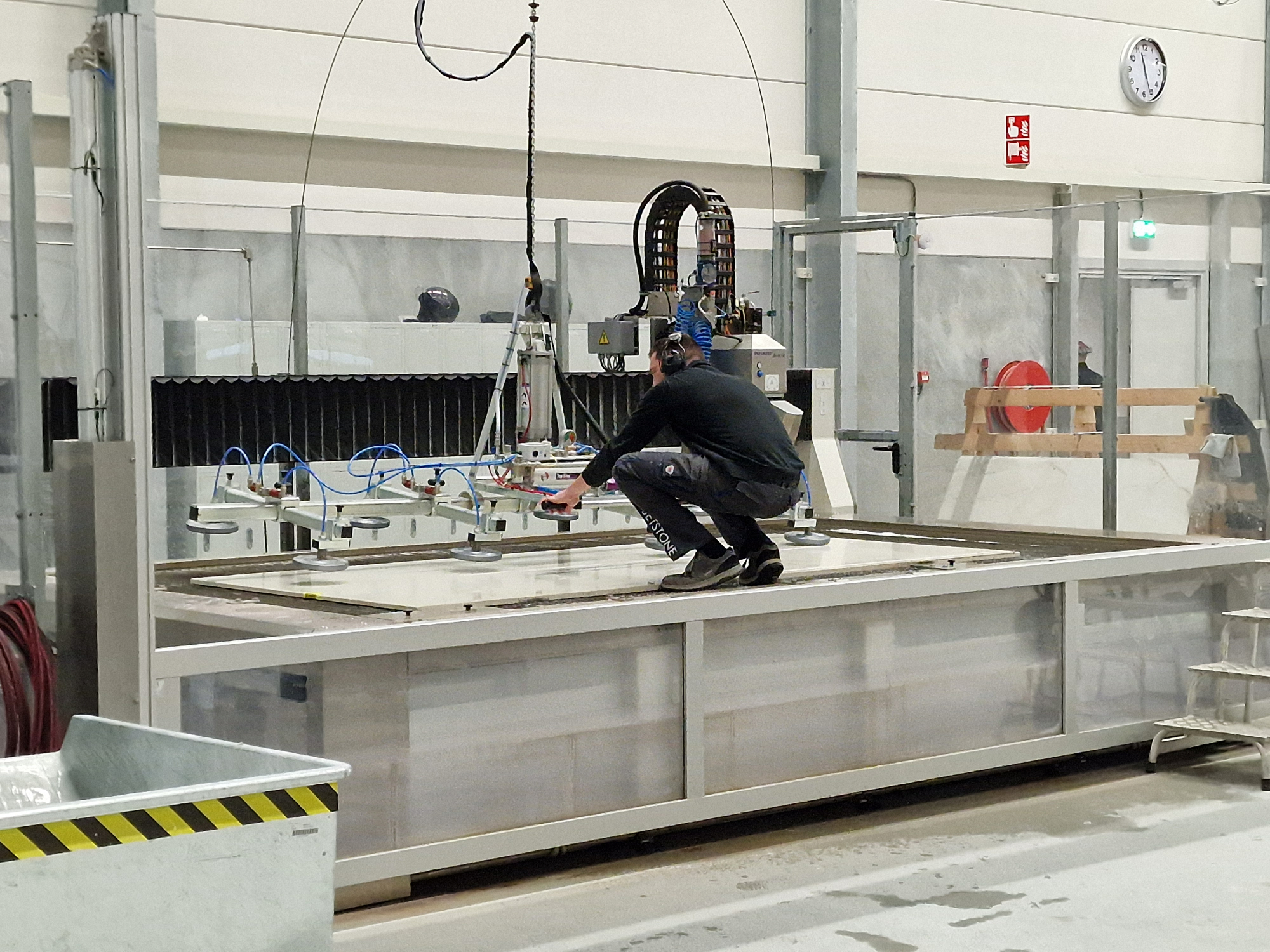
Eerste fabriek
De productielocatie op de boerderij werd al snel te klein. Helemaal toen Jetstone naast natuursteen ook kwartscomposiet ging gebruiken voor de productie van keukenbladen. “In 1996 opende Jetstone de locatie aan de Florijn in Deurne. Ik kan me die tijd heel goed herinneren, omdat sinds de oprichting altijd op de achtergrond betrokken en geïnteresseerd geweest in het bedrijf van mijn vader. Op zaterdagen en in de vakanties in de periode 1993 tot en met 1999 hielp ik altijd mee. Ik koos er echter voor om eerst een opleiding tot accountant te volgen en in die sector aan het werk te gaan. Sinds 2004 werk ik bij Jetstone als directeur”, aldus Van de Heuvel.
Omdat de focus steeds meer op de internationale markt kwam te liggen, werd aan de Beukelsdijk in 2012 een nieuwe productielocatie erbij geopend. “Deze is in 2018 met een extra hal uitgebreid, waarmee we een enorme stap hebben kunnen zetten qua capaciteit. We waren voorbereid op de toekomst”, vertelt Van den Heuvel. Hij wist toen nog niet hoe noodzakelijk de uitbreiding was. Dan kwam met de uitbraak van Covid. “Dat leverde een enorme golf aan opdrachten op. Mensen gingen door de pandemie niet of minder op vakantie en investeerden veel in de eigen woning. De focus kwam op dure en luxe producten te liggen. Dat leverde voor ons qua omzet pure bonusjaren op. Het bleek ook niet een eenmalige ontwikkeling, maar meer en meer een cultuurwijziging. Ook door meer aandacht voor duurzaamheid, hetgeen een positieve ontwikkeling opleverde voor steenachtige keukenbladen in vergelijking met kunststof aanrechtbladen. Hele ketens als Center Parcs hebben deze metamorfose voor hun bungalows ingezet”, aldus Van den Heuvel.
Donkere kanten
Maar het was niet allemaal crescendo voor het bedrijf uit Deurne. In het rapport ‘The Dark Sides of Granite’ van onder andere de Landelijke India Werkgroep (LIW) uit 2017 werd Jetstone genoemd. “Het rapport ging over kinderarbeid, slavernij en onveilige werkomstandigheden in Indiase granietgroeven. Wij werden als een van de bedrijven genoemd die zaken deden met groeves waar misstanden waren geconstateerd. Wij zijn echter niet in Ierland gevestigd en ook nooit geweest – zoals in het rapport stond – én wij deden geen zaken met het genoemde Indiase bedrijf, eigenaar van de granietgroeve. Uiteindelijk zijn deze zaken gerectificeerd, maar het zorgt natuurlijk niet voor een positieve pr. Overigens werken we nu goed samen met Arisa, de ngo die het werk van LIW heeft overgenomen”, legt Van den Heuvel uit.
De tweede tegenslag had een enorme impact op Van den Heuvel en de medewerkers van Jetstone, vertelt de directeur van het Deurnese bedrijf. “In oktober 2020 overleed een medewerker toen een bok platen omviel. Dat hakte er behoorlijk in bij ons. We hadden op plekken waar met hele platen werd gewerkt gele palen geplaatst, om medewerkers er alert op te maken. Op de plek waar het ongeval plaatsvond stonden echter nog geen gele palen. Nu hebben we op al onze drie locaties gele palen geplaatst waar risico gelopen kan worden, in totaal zo’n zestienhonderd. En bij de inrichting van de nieuwe hal hebben we ook maatregelen genomen”, zegt Van den Heuvel en hij voegt er nog aan toe dat hij die tijdens een rondleiding zal laten zien.
De meest recente tegenslag waarmee het bedrijf uit Deurne mee kreeg te kampen, ontdekte medewerkers van Jetstone bij toeval. “We werden het slachtoffer van een cybercrime-aanval. De update van de virussoftware op die dag verliep niet naar behoren. Toen we dat gingen onderzoeken, kwamen we erachter dat de besturing deels was overgenomen. We hebben de server direct stopgezet en zijn overgaan op handmatige bediening en besturing. Twee weken lang hebben we zo gewerkt en in die tijd hebben we de betreffende systemen schoongemaakt en waren we weer operationeel. Een helse twee weken, maar alles is goed gekomen.”
Custom made
Bij binnenkomst van de nieuwe productiehal valt direct op dat de keramische platen en de platen van kwartscomposiet – de materialen waarmee Jetstone het meeste werkt – horizontaal op elkaar opgeslagen liggen. “Ons platenmagazijn is afkomstig uit de houtsector”, begint Van den Heuvel zijn uitleg. “Vrijwel alle platen zijn horizontaal opgeslagen. Vanuit het magazijn worden ze via een custom made aanvoersysteem naar de zaagmachines getransporteerd. Is een plaat nodig die bijna onderop de stapel ligt, dan worden automatisch alle bovenliggende platen aan de kant gelegd, de juiste plaat op de transportband gelegd en vervolgens worden de andere platen weer terug op de stapel gelegd. De keramische platen worden naar een van de drie productielijnen getransporteerd, waar ze na de zaagwerkzaamheden naar de verdere bewerkingen worden vervoerd. Dit gebeurt via vacuümheffers die door medewerkers worden bediend, omdat de keramische platen eerst gezaagd moeten worden en daarna pas gepolijst. De platen zijn namelijk kwetsbaarder vanwege hun geringe dikte. De productielijn voor de kwartscomposietbladen is volledig geautomatiseerd. De platen worden eerst automatisch gepolijst en vervolgens gezaagd. Medewerkers komen na alle bewerkingen pas in aanraking met de platen en lopen dus ook vrijwel geen risico.” Van den Heuvel hint hiermee op de actuele ontwikkelingen in Australië en de Amerikaanse staat Californië waarbij onder andere het bewerken van kwartscomposiet producten aan strenge maatregelen is onderworpen. In Australië zelfs geleid tot een algeheel verbod. “Wij doen er alles aan om onze medewerkers onder zo veilig mogelijke omstandigheden te laten werken. Daartoe hoort ook een personeelsmonitoringsysteem wat het stof betreft. De resultaten van de periodieke controles worden in een laboratorium geanalyseerd en waar nodig worden aanpassingen in de fabriek aangebracht. Met dit meten zijn we al in 2005 begonnen.”
Jetstone Academy
Verderop in de nieuwe productiehal vinden de handmatige bewerkingen plaats. Een jonge vrouw is de kanten van een keukenblad aan het polijsten. “Er werken bij ons relatief veel vrouwen”, vertelt Van den Heuvel. “Het is schoon en veilig werken en de productie is zo veel mogelijk geautomatiseerd. Dat spreekt mensen aan. Zo’n 90 procent van onze medewerkers zijn afkomstig binnen een straal van twintig kilometer.”
Na de Covid-pandemie heeft Jetstone veel mensen moeten omscholen. “Mensen die uit sectoren kwamen die harde klappen hebben gehad door corona, bijvoorbeeld de horeca. Er werken dankzij onze Jetstone Academy meer bakkers dan in een bakkerij in de omgeving en meer koks dan in een restaurant. Ze hebben allemaal een programma doorlopen dat we in een app aanbieden, in verschillende talen zoals Nederlands, Engels en Pools bijvoorbeeld. Elk onderdeel wordt afgesloten met een soort quiz”, vertelt de directeur terwijl hij het programma demonstreert op zijn telefoon.
In deze tijd van krapte op de personeelsmarkt is het zaak om medewerkers binnen boord te houden, beseft Van den Heuvel. “Wij doen er alles aan om ze aan ons te binden. We willen een echt FAMILIEbedrijf zijn, je ziet je medewerkers immers vaker dan je eigen familie, ze zijn een stuk van je familie. In de nieuwe kantine wordt voor de jongere medewerkers een gamehoek ingericht, de oudere kunnen de strijd aan het dartbord aangaan. Het streven is dat januari 2025 alles is ingericht op de nieuwe locatie”, besluit hij de rondleiding.
Circulair
Bij het ontwerp van de nieuwe bedrijfshal van Jetstone heeft duurzaamheid een grote rol gespeeld, benadrukt Van den Heuvel. “CO₂-reductie is niet alleen voor ons van belang, ook voor onze klanten is het een steeds belangrijker item. Daarom is onze nieuwe locatie circulair gebouwd. De stalen constructie en de wandpanelen zijn demontabel en her te gebruiken, we zijn volledig elektrisch, dus zonder gasaansluiting, en de stroom wordt opgewekt door zo’n 3800 zonnepanelen die op de daken liggen. Dat past perfect binnen onze toekomstvisie: op een duurzame en veilige manier keukenbladen produceren. En we kunnen nog groeien. We hebben nu drie productielijnen in gebruik en hebben nog plaats voor nog vier complete lijnen.”
- Bekijk ook
- www.jetstone.nl